PelletSave Installation During Covid-19 Pandemics
We are excited to announce the delivery of another PelletSave, a central blending system, to a big customer in Europe. The system is intended for a plastic garden furniture manufacturer. It provides a complete blending solution to 30 injection machines on the production floor.
Due to Covid-19 limitations, we will not be able to send a representative on our behalf for installation. Since this is the first time the installation of such a central system takes place without the presence of our representative, we have prepared a special installation manual. It contained explanations, 3D drawings and pictures. The customer with the help of our instructions and remote support, will carry out the assembly.
Before shipment, we invited large customers from the local industry. They could see, touch and impress themselves with the system. Indeed, many customers took the opportunity to train towards future orders and to ask questions.
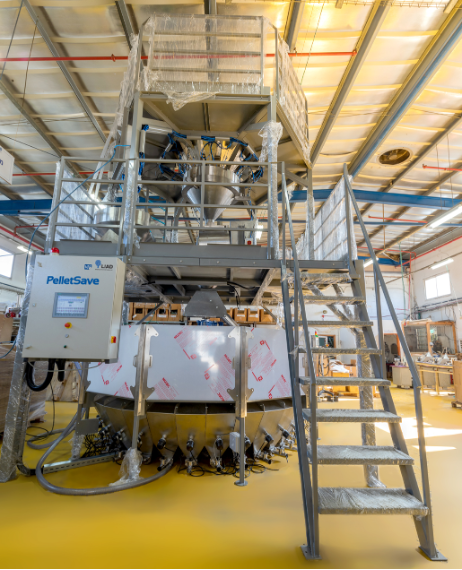
PelletSave system at LIAD before delivery to the customer
PelletSave – a central gravimetric batch blending system
PelletSave is a 12 channels central batch blending system for preparing batched with a sequence weighting system. It sends out the mixtures to each of the various machines on the production floor with high precision levels. Together with a sophisticated control system, PelletSave can feed up to 50 processing machines, such as extruders, injection molding or extrusion blow molding machines.
The system has many advantages, including:
- Save of space on the production floor: the area that the system occupies is minimal. The place of its location does not have to be central.
- Data collection and record of production: collecting data about materials consumption in the entire plant is a difficult task to perform. The materials are usually not weighed before and local batch blenders are often old. This is far from the vision of Industry 4.0 and does not reflect the need for production floor visibility for all functionaries. At LIAD we have invested great efforts in order to provide a a suitable solution. With the use of PelletSave, it is possible to store all the raw material consumption data of the plant in one central place. One can transfer this data to the MES and ERP systems. This, among all, provides an accurate view of which mixture arrived at which machine and when.
- Combination of recycled raw materials: the large amount of raw material channels allows the use of raw materials of different qualities including recycled ones. For each individual machine the relationship between the different raw materials is controllable. For example, the percentage of recycled material can be higher in less sensitive products in order to reduce production costs. This flexibility is not possible in any kind in local batch blending systems with a small number of channels.
- Saving manpower and reducing human errors: The implementation of PelletSave system eliminates the need in manual preparations. Moreover, manpower can open the door to human error in the blend materials. This can lead to quality problems for the end customers and to damaging their trust in the supplier.
- Vacuum conveying optimization: Local batch blending systems require the use of long piping in order to route all the raw materials separately to each machine. The use of a central blending system reduces the size of the overall length system of the piping. Also, it reduces a number of receivers and simplifies the vacuum system.
More information about the PelletSave system can be found on the product page on our website.
Is it possible to install the PelletSave system to an existing factory?
The PelletSave system is significantly cheaper than many local batch blending systems. Considering the vacuum system cost reduction, the system is even more affordable. PelletSave system installation pays off not only for a new plant but also for existing plants such as the European plant to which the latest system was sent. Infrastructure changes are not major and its benefits lead to savings in the production process and to a quick return on the investment.